When observing narrow spaces that cannot be directly visualized by the human eye, we use an ‘endoscope.’
Among them, the most well-known is the ‘fiberscope,’ but endoscopes come in various types, not limited to fiberscopes.
In this article, we will introduce the features of fiberscopes and other types of endoscopes to help you choose the right one for your needs.
1. Fiberscopes and Endoscopes
Many people might think that “Fiberscope = Endoscope.”
Fiberscopes are indeed one type of endoscope.
Back when camera miniaturization was not feasible, fiberscopes dominated the field of endoscopy. Consequently, they became synonymous with endoscopes.
Currently, fiberscopes are widely used for observations with diameters below φ1mm. Due to their relatively high cost, for diameters above φ1mm, people often opt for other types of endoscopes.
2. Characteristics of Fiberscopes
(1) Đường kính siêu mỏng cho phép quan sát các lỗ nhỏ hơn φ1 mm
The primary feature is, indeed, its thinness.
Since each fiber has a camera attached to its tip, there are various options for outer diameters.
The thinnest diameter possible is around φ0.35mm, and fiberscopes with diameters above φ1mm are also available for purchase.
(2) Structure of Fiberscopes
Fiberscopes consist of extremely thin fibers bundled together, with small lenses attached to the tip for internal observation.
However, due to the structure of bundling thin fibers, shadows of the honeycomb structure may be visible. (It’s possible to eliminate these shadows by capturing the observation image with a camera and applying image processing, but in doing so, the image may become slightly blurred.)
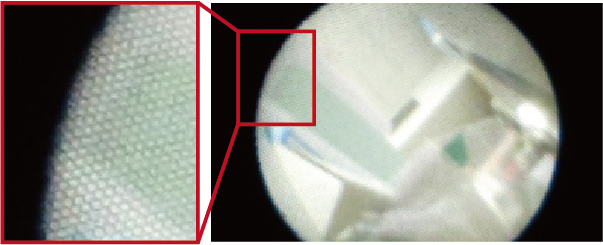
(3) Can be used in narrow, winding spaces
Since fibers are used, they can be inserted into the interior of winding pipes or into tight spaces within intricate machinery.
– Caution is required when handling!
The fibers are made of highly transparent materials such as quartz glass or plastic, so applying strong force to the fiber part or reducing the bending radius too much can cause the fibers to break.
(4) Not suitable for long lengths
By adjusting the length of the fibers, it’s possible to observe inside long pipes. However, since light (image) passes through the fibers, extending the length will proportionally darken the image. (This is due to losses from reflection within the fibers.) Additionally, because fibers themselves are expensive, the price increases proportionally with length.
◆ Capable of Observing Below φ1mm! Recommended Fiberscopes
By using an adapter lens, it’s possible to connect to a camera and observe on a PC or monitor.
3. Other Types of Endoscopes
(1) Endoscopes with Built-in Front Camera
Currently, there are many types of endoscopes available for sale, widely used in various fields. These endoscopes feature a small camera and lighting enclosed at the tip.
Our MIGS series corresponds to this type of endoscope.
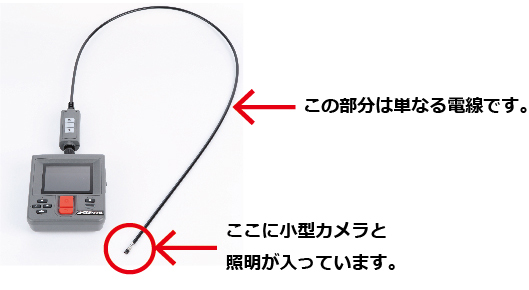
<Advantages>
– Among endoscopes, relatively affordable due to the absence of special lenses or fibers. (*There are also high-end types with additional features.)
– The relay part consists of wires, allowing for greater flexibility than fibers. Additionally, long-length types are available.
– As it’s simply a camera, it can be adapted for various applications.
(*See below for details)
<Disadvantages>
– Resolution depends on the camera. (Resolution worsens as the camera size decreases.)
– Due to the size of the camera (sensor) and LED chips, it’s not possible to achieve the same thinness as fiberscopes or borescopes. (Minimum around φ1.8mm)
– Focus depends on the camera’s focal length, so it may not focus properly on close-up parts. (Minimum focusing distance: approximately 10mm to 15mm)
2) Borescopes (Rigid Endoscopes)
A borescope consists of multiple rod lenses enclosed in the tip of a stainless steel tube, designed to focus at the eyepiece (end).
Most borescopes have a basic shape similar to the following:
⇒ You can find Shodenshadensha’s borescope series here.
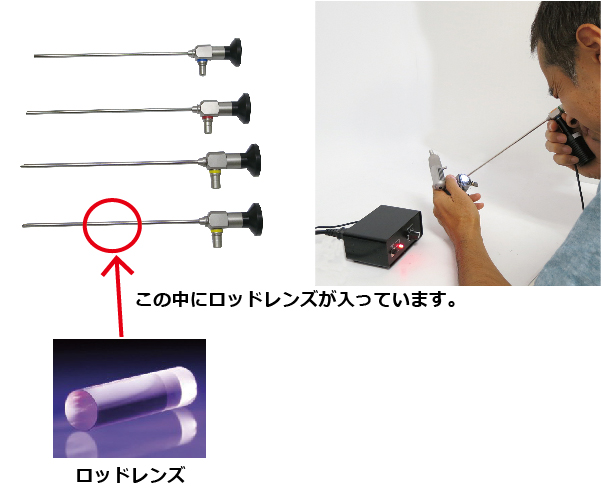
– It’s also possible to observe on a PC or monitor!
While the premise is for direct viewing, connecting a camera using an adapter lens allows for observation on a PC or monitor.
◆ Borescope, Adapter Lens, Camera Integrated as One!
Recommended Borescope Camera System
We also offer sets like “High Definition Camera + Camera Adapter + LED Light Source” as well as standalone options such as “Adapter Lenses” and “Borescope Dedicated Cameras”.
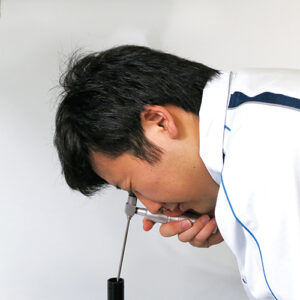
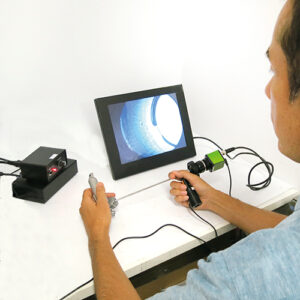
You can find Matsudensha’s borescope camera systems and options here: [link]
<Advantages>
– Image is sharper than with fiberscopes.
– It can observe objects at close proximity. (With a bit of adjustment, focusing can be achieved at around 3mm.)
– While not as thin as fiberscopes, it’s still capable of narrow diameters. (Our borescopes offer minimum diameters of around φ0.7mm.)
– Since there are no electronic devices such as cameras in the borescope part, it can be tailored for waterproofing, heat resistance, saltwater resistance, chemical resistance, etc. (Our products include standard heat-resistant types up to 120°C.)
<Disadvantages>
– Cannot be custom-made to any length due to the need to focus with multiple lenses.
– Cannot be bent due to the structure of glass lenses in stainless steel tubes.
– Glass lenses lack resilience against impacts or bending stress. (While not as resilient as larger diameters, they are durable with careful handling.)
– Generally, it’s more expensive than standard endoscopes with built-in cameras. (If used for direct viewing without connecting a camera, the price decreases.)
Summary
Many people might think that “Fiberscope = Endoscope,” but in fact, a fiberscope is just one type of endoscope.
There are various types of endoscopes, including:
– Fiberscopes
– Endoscopes with built-in front cameras
– Borescopes (rigid endoscopes)
Each has its own advantages and disadvantages, allowing you to choose the one that best suits your needs.
At Matsudensha, we offer a wide range of products, including the endoscopes mentioned here. For more details, please visit our product page below.
If you have any difficulty choosing an endoscope, please feel free to contact us via the inquiry button at the bottom of the page.